Total Quality Management (TQM)
The challenge that companies face as the 21st Century gets underway, is to succeed in a global economy where competition is fierce and where customers are becoming increasingly demanding of quality. Companies must supply products and services that are competitive in both price and quality, and in international as well as in domestic markets.
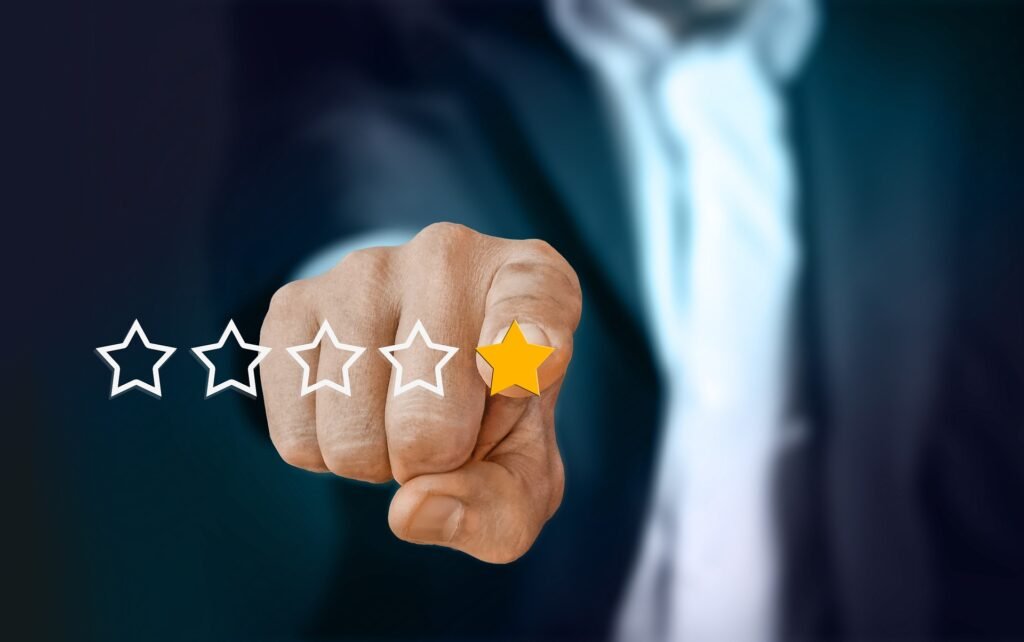
maintain a competitive edge in such an environment they must continually improve the quality of what they offer. Total Quality Management (TQM) is a management strategy, which has proven itself as a way of managing and continuously improving quality. Its successful implementation in Japanese firms has been a major factor not only in their success, but also in establishing the levels of quality that customers now expect in whatever they purchase.
Course Benefits
- Extended ownership of the business processes to each employee by empowering them to improve organizational performance
- Improved organizational culture, intrinsic motivation and atmosphere of enthusiasm & satisfaction among the workforces
- Increase of sales through better product/service and new product/service development
- Quality improvement by reduction of market claims and defects in the process
- Reduction of cycle time through productivity improvement
- Reduction of accident through safety operation
- Reduction of non-conformance, repairs and reworks
- Increase of employees’ suggestions and QCC activities
- Process efficiency leading to improved profit per product and service
Course Outline
Fundamentals of Quality and TQM
- What is Quality in the Competitive Business World?
- Conformance and Non-Conformance Costs of Quality
- Dimensions of Product And Service’ Quality
- Evolution of Modern Concepts of Quality
- Definition and Understanding of TQM
- Importance of TQM in Overall Supply Chain Operations of any Organization
SWOT Analysis
- What is SWOT Analysis?
- Objectives of SWOT Analysis?
- The Four Generic Strategies From SWOT Analysis
Problem Solving Tools and Techniques
- PDCA Approach
- 7 QC Tools
- SIPOC Diagram
Principles of TQM
- Total Employee Engagement.
- Kaizen Culture
- Kano Model to Prioritize Customer Requirements.
Kaizen Through Quality Control Circle
- Revolution of Quality Control Circle in Japan
- Objectives Quality Control Circle
- National and International Convention on QCC
This course is for
Top, Mid-Level, and Ground Level Executives, who are interested to bring improvement in their work or business. Senior level executives are highly encouraged to join in the session who have the authority and capability to implement the concept.